Elea stories
What our customers say about us
Every customer story is important to us
Every PEF solution we create is uniquely designed to meet the specific needs of our clients. Here, we showcase real-world success stories, highlighting how our innovative PEF technology has transformed their production, enhanced efficiency, and unlocked new product opportunities. Explore their journeys and discover what Elea PEF can do for you.
Amica Chips, Italy
Amica Chips installs four Elea B 1 PEF systems for yield and quality improvement
Company Background
Amica S.p.A. is a potato chip manufacturer based in Castiglione delle Stiviere, Italy. The company was founded in 1990 by Alfredo Moratti and Andrea Romano and has since grown into a leading player in the potato chips market. With more than 250 employees, Amica exports its products to over 20 countries.
Improved slicing and frying at lower temperatures
In early 2020, Elea and Amica began their collaboration with a trial installation on an industrial-scale production line. The tests demonstrated key benefits of PEF technology, including improved slicing precision, better cut consistency, and the potential to reduce heat load during frying.
Enhanced cutting led to reduced breakage and fines, as well as lower starch loss in processing water. Additionally, a shorter frying time and lower temperature resulted in a lighter, higher-quality product. The smoother surface of the slices also led to reduced oil absorption, better seasoning adhesion, and a crunchier texture.
In this video, Mr. Franck Bianchi, Plant Manager of Amica Chips in Italy, talks about his motivation and experience in installing an Elea PEF Advantage Belt system into the Amica chips production line.
We have used this testimonial in our PEFinar on "Fry the perfect chip with PEF" - Thank you very much Franck, we are very happy about our collaboration and your kind feedback!
Full-Scale implementation
Following successful testing in the autumn of 2020, Amica Chips installed its fourth Elea PEF Advantage B 1 system. These units have a processing capacity of up to 6 tonnes of tubers per hour. The installation and commissioning process proved to be quick and straightforward. Despite the challenges posed by the pandemic, Elea and Amica’s engineering and applications teams successfully utilised both remote and on-site tools to complete the project efficiently.
The video shows the Elea PEF Advantage B 1 installations at Amica Chips SPA in Castglioni delle Stiviere.
Reduce costs, increase yield, control colour, improve quality and develop new product opportunities with our Elea PEF Advantage Belt systems.
Frozen Express, Columbia
Elea PEF Advantage B 10-320 for larger fries in different shapes with better quality and reduced processing costs
Family Legacy
Frozen Express is one of Colombia’s largest processors and manufacturers of frozen French fries. As a proud family-owned business, they have been delivering high-quality potato products for over 25 years while remaining committed to supporting Colombian farmers.
Embracing Innovation
In August 2021, Frozen Express upgraded its production line by installing an Elea PEF system. This innovative technology was introduced to produce larger fries in a variety of shapes, improve overall quality, and reduce production costs.
Guillermo Fonseca, Engineering Manager at Frozen Express, explains, “We chose to use PEF to enhance our lines and produce better food with fewer resources. Elea was the best choice for us, thanks to their extensive experience, strong credentials, and excellent technical support.”
Elea was the best choice for us
Working alongside Ignacio Alonzo, Elea’s representative in Colombia, Frozen Express installed an Elea PEF Advantage B10 -320 system. This advanced system efficiently handles production capacities ranging from a single tuber up to 12 tonnes per hour, with Alonzo providing on-site installation support and collaborating closely with Frozen Express technicians.
Expert partnership
Efficiency, Quality, Sustainability
The Elea PEF technology replaces traditional preheating of potato tubers, significantly reducing water and energy consumption. Moreover, it enhances the cutting process, leading to improved product yield and quality. Installed prior to the hydrojet cutting stage, this low-heat, energy-efficient process softens the tissue and ensures more precise cuts.
With this innovative upgrade, Frozen Express continues to set high standards in the frozen French fries market, blending tradition with cutting-edge technology for a brighter, more sustainable future.
Kanaan, Croatia
Higher quality chips, better crunch, improved cutting and reduced oil uptake of 3% with Elea PEF Advantage B 1
About Kanaan
Kanaan is Croatia´s largest snack products manufacturer, producing hand cooked chips, popcorn, corn flips, rice snack, popcorn snack as well as potato chips. The company has been established in 1990 by its owner and director Zvonko Popović.
Testing with Elea
Kanaan and Elea have run a test project with an Elea PEF Advantage system to evaluate PEF impact on product yield and quality. After successful testing a line upgrade has been conducted and a state of the art Elea PEF Advantage B1 system has been installed.
Tomislav Lukacevic, Project Manager at Kanaan, stated: “The cooperation with Elea has been very fruitful. Product quality is of high importance to us, which is why we have invested in an Elea PEF system. We have observed numerous PEF-induced benefits in our potato chip processing line, leading to higher product quality and a better crunch. The improved cutting has resulted in a 3% reduction in oil uptake.”
Cooperation with Elea lead to higher product quality and process efficiency
Jimmy Kinsella, Engineering Manager at Elea, added:
“We are proud to work with Kanaan. The cooperation has been highly professional from the early-stage discussions to installation and startup.”
A Strong Partnership
Elea’s Advanced PEF Solutions
Elea has developed a compact, all-in-one design for potato and vegetable chip processing, with treatment capacities ranging from 1 to 10 t per hour. For larger-scale processing, continuous systems with capacities of up to 100 tonnes per hour are available.
The benefits of PEF technology for the potato chip industry include improved cutting quality and yield, reduced frying time and temperature, and lower oil uptake, all contributing to enhanced product quality and efficiency.
Two Elea PEF Advantage B 1 systems enhance slicing, frying and overall product quality
Liwayway, China
A Leading Snack Company in Asia
Liwayway (China) Co., Ltd., known for its brand Oishi and an extensive range of over 100 product varieties, is one of Asia’s leading snack companies. From its humble beginnings producing “gawgaw” (starch) and coffee 70 years ago, the company has embarked on ever more ambitious and exciting ventures.
A Strong Partnership for the Future
In 2021, Liwayway installed its first Elea PEF Advantage B1 system in its potato chip production line, working in close collaboration with Elea’s regional partner for China, Beijing Lenno Trade Co., Ltd.
At Elea and Lenno, we are honoured and proud to collaborate with the Liwayway (China) Co., Ltd. team, supporting their commitment to innovation and excellence in snack production.
The integration of Elea PEF technology has provided Liwayway with several key benefits, including improved slicing performance and yield, reduced frying time and temperature, lower oil absorption, and enhanced final product quality.
Encouraged by these advantages, Liwayway has installed a second unit in 2022.
Promising Production Benefits lead to 2nd B 1 System
LENNO Test Center in Beijing
Beijing Lenno Trade Co., Ltd. is a professional agency for advanced food processing machinery, imported from Europe and North America and Elea’s exclusive agent for the Chinese market.
In 2021, Lenno established an over 800 sqm demo centre and testing lab in its Beijing office. It is currently equipped with Elea’s PEF Advantage B1 system, varieties of FAM cutters, and other demo machines of imported food processors.
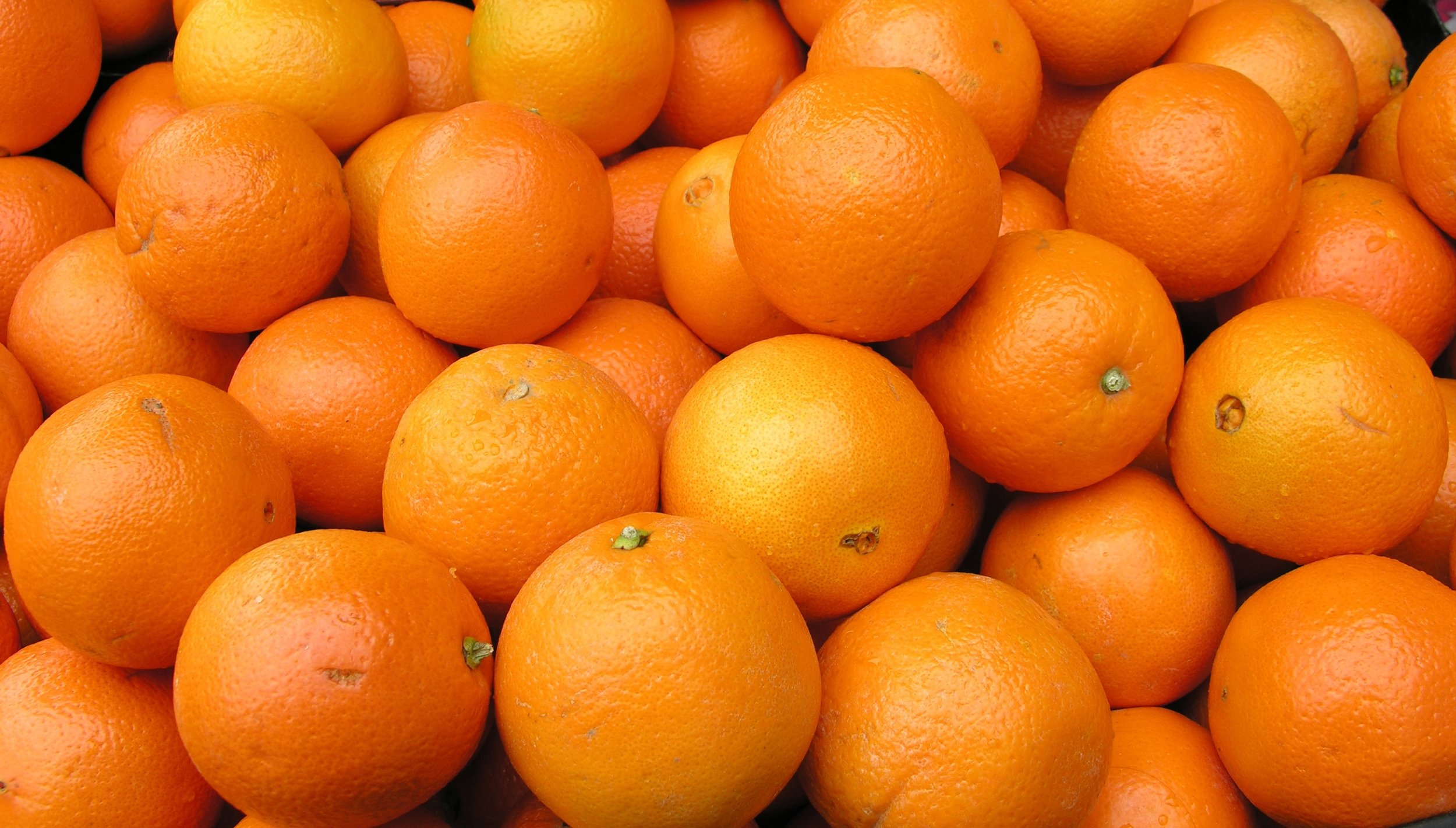
Hoogesteger, The Netherlands
Extending shelf-life and preserving the juice quality
A Pioneering Application of PEF Technology
Since 2012, Hoogesteger has been a shining example of industrial innovation, using Pulsed Electric Field (PEF) technology—branded as Fresh Micro Pulse (FMP)—to extend the shelf life of fresh juices and expand market reach. The Dutch premium fruit juice supplier has taken on a pioneering role in integrating this cutting-edge technology into its production lines.
Extending Freshness, Expanding Opportunities
By implementing Elea PEF systems, Hoogesteger has successfully increased the shelf life of its juices from 6–7 days to an impressive 21 days. This advancement has not only improved product longevity but also enhanced market distribution and streamlined production planning.
As a continuously operable system, PEF technology provides flexibility in processing capacities and supports bottling into various packaging formats and materials, making it a versatile solution for modern juice production.
Efficiency and Flexibility in Production
Preserving Quality with Gentle Processing
PEF technology operates at low temperatures, ensuring that the juice maintains its fresh taste, vibrant color, and full nutritional value—all while consuming minimal energy.
Learn more about Hoogesteger’s process here: Hoogesteger – Our Process
Some of our clients and partners
Many of our clients require strict confidentiality about their PEF solution so a special thanks to those who have let us use their logo and shared their experience with Elea Technology with the world.
Prof.-von-Klitzing-Str. 9, D-49610 Quakenbrück, Germany
Hours
Monday–Friday
8.00 - 17.00
Phone
+49 (0) 5431 92629 70